“That’s our cover,” said Sara Gullickson, CEO of Item 9 Labs, which sells medical-marijuana products in 37 dispensaries in Arizona.
Not only does the dairy farm obscure the already faceless warehouse of a stigmatized industry, but no one has odor complaints about the nearby cannabis-growing facility east of Casa Grande.
Everyone entering the facility, including reporters, get sprayed below the knees with disinfectant, down to the soles of shoes. It’s a precautionary measure against bringing bacteria into the warehouse. The tour started from there.
In one room near the front of the building, employees trimmed flower over stainless steel tables. Sticky notes at the end indicate which strain they’re working on: Blue Dream, Girl Scout Cookies or Jack Herer.
Hundreds of cannabis plants relaxed in a harvest room, which looked like a forest of blended shades of green bathed in high-pressure sodium lights. Tall, bright green plants bloom in the center of the room — that’s the sativa Jack Herer, its fragrance light and fruity. Next to it are smaller, darker Girl Scout Cookies, an indica, which have a noticeably earthier, pine-tree-like smell.
Plants spend between 60 and 75 days growing their buds once they’re in the flowering stage. The whole process, from the time plants hits the soil, takes 60 to 100 days. Item 9 has three grow rooms, each with plants at various stages of growth.
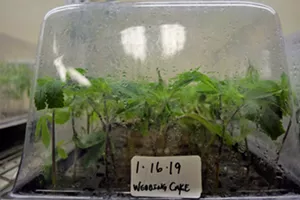
Freshly trimmed from the mother plant, baby cannabis plants take root inside mini-greenhouses.
Nick Meyers
The whole process starts with mother plants, which ensure the same genes are used in every batch. These plants are noticeably wider and branchier than the plants that get harvested.
The plants spend their adolescence in the nursery at the end of the hallway. Clippings from the mother plant are placed in small pots where they start to form root systems.
Along one of the nursery walls sits a rack of trays with plastic covers that act as green houses for the developing plants.
Once growers begin to recognize new leaves sprouting from the plant, usually in seven to 10 days, they know it’s time to move the plant to a bigger pot.
From there, the plants are moved to bigger pots where roots develop and branches begin to grow. In a month or two, depending on the strain, the plants have big enough branches to bear big juicy buds.
At one end of a hall are three shipping containers where the plants go to dry cure after they’re harvested. Branches from the plants hang upside-down from chicken wire, which is replaced every other month.
The plants spend about two weeks curing.
In the beginning, during the learning stages, Item 9 grew 30 strains. As they experimented, they worked their way up to 97. Eventually they settled on 45 favorites, but they’re constantly developing their strains.
“But you’ll always have your core,” Skalla said. “There’s always going to be five to 10 strains that your patients always need.”
Across from the curing rooms is the lab, where workers process flower into concentrate after it’s trimmed.
A chemistry set like something out of an old sci-fi movie sits on top of a stainless-steel table in the middle of the room. The distillation device removes terpenes from plant matter that will be added later to cannabinoid extract to make live resin, a hot product right now.
Next door to the converted warehouse, its twin is being constructed. Each of the grow rooms in the new facility are expected to produce 50 to 60 pounds of product each month, Skalla said.
Item 9 is comfortable at its home location, and Pinal County is happy to have it — it’s committed to 30 percent local employment.
“But they wouldn’t let us sponsor a Little League team this year,” Skalla said. “We did try.”
See more photos from the tour below: